Taking Customer Approach to the Next Level
At Tasowheel, we pride ourselves on delivering precision solutions that meet our customers’ unique needs, reflecting our core value of customer focus.
Recently, we had the pleasure of working with VPK Group, a Belgian paper and cardboard company specializing in manufacturing corrugated cardboard packaging from recycled paper. VPK Paper’s Oudegem mill approached us for an upgrade of their PM7, following the effective completion of a slice profiler project on their PM6 in 2020.
The Upgrade: Our Step-by-Step Approach, Partial Delivery
The customer was facing problems with aging actuators and obsolescence of spares. Their wish was to phase the dilution system replacement in several stages to smooth out costs. Tasowheel was the only supplier for this, while competitors were requesting to make a single upgrade all at once.
“Our solution enables both the original and new actuators to operate side by side, with setpoints linked similarly to ensure smooth integration. For the operators, there’s no difference in display interfaces, which helps maintain ease of use.”
Mikko Kinnunen, Business Director
Characteristics and Benefits
Investment Management: By delivering in parts, the customer can spread out their investment over time, easing financial strain.
Critical Parts Replacement: This approach allows the customer to replace only the malfunctioning actuators at their discretion.
Low Risk: The gradual implementation minimizes risk, providing a smooth transition from old to new systems with the help of preparation work before the shut down. This results in a shorter down time.
Spare Parts Availability: Enhanced availability of spare parts ensures ongoing and future operational efficiency.
Mutual Trust and Customer Orientation
Integrating our actuator system with the customer’s existing infrastructure was a critical aspect of this project. Despite the challenge posed by aging competitors’ actuators with no available spares, we tailored our solutions to perfectly replace the obsolete components. The startup of the new system required only minor remote assistance from us, while customer took the most responsibility of the commissioning work. This showcases the effectiveness of our upgrade and the strong trust we have built with VPK paper.
Eric Garcon, Reliability Engineer, shared his satisfaction with the project:

“The system is functioning smoothly, and we appreciate excellent collaboration and Tasowheel’s customer approach. With the preparation work carried out beforehand, we have regained control over many actuators, which had not happened for more than six months. Thank you once again for your flexibility.”
-Eric Garcon, VPK
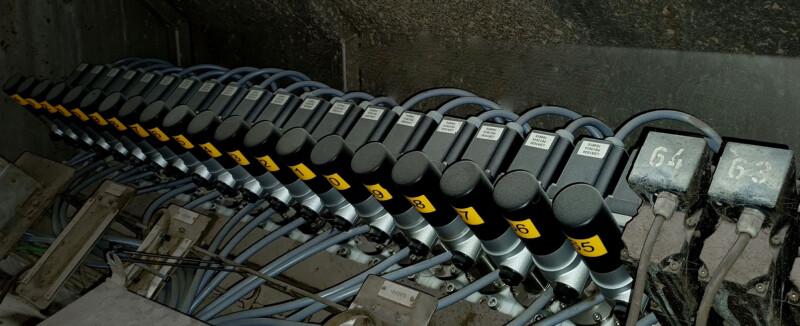
With the first set of actuators successfully delivered and integrated, the next set is already on its way, continuing our phased upgrade approach.
